Pumice stones have a long list of limitations with all the said benefits. The way stone works may damage the garment and washing machine itself due to their higher abrasion. It leaves stone dust in the garments and in pocket bags, which adds extra rinsing and manual pocket cleaning operations. Moreover, It causes back staining and re-deposition.
It’s time to think of a stone alternative that minimizes these limitations. A project was taken to run a trial in Crown Washing Ltd. with Soko stone-free concept.
Experiment:
A team was formed to do the innovation project. Binoy Chandra Halder, a Student of Daffodil International University, was this project’s executor. Moniruzzaman Babu, Production GM, Crown Washing Ltd., was Industry Supervisor, and Md. Forhad Hossan, CEO of Pure Chemicals, was the Industry Expert for this project.
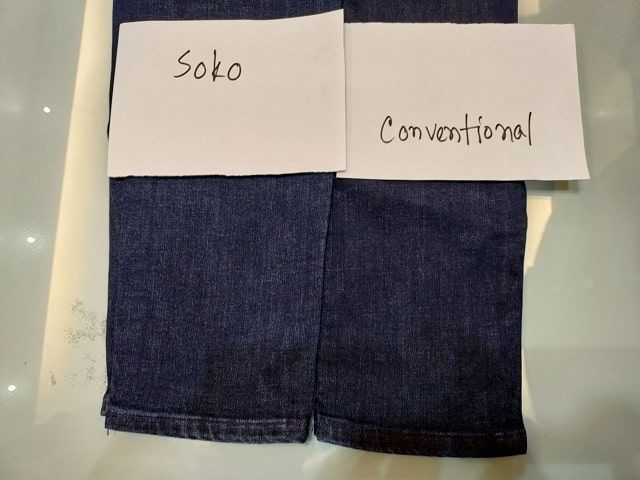
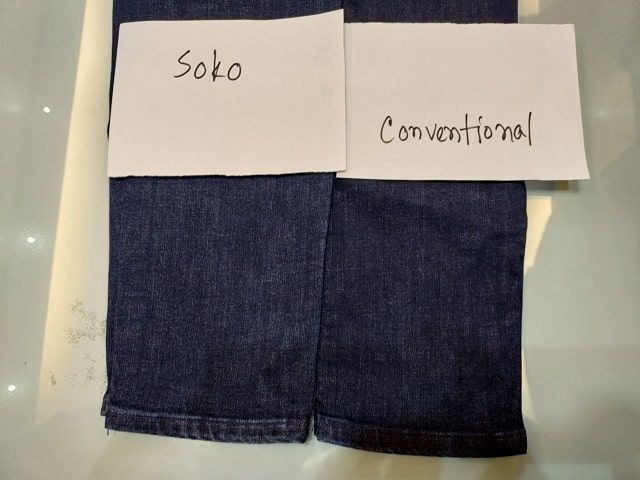
Figure 1: Abrasion effect with Soko and in the conventional method.
A trial was conducted on 100 kg bulk in the conventional process and a 100 kg bulk in the proposed method. Since the rest of the washing process is the same, key differentiating segments of the conventional process and proposed process (with Soko stone-free concept) is mentioned below-
Process comparison of enzyme wash for 100 kg garments (200-250 pcs):

Result: The result found in the above experiment and impacts are noted below-
More contrast and hi-low: With Soko’s stone-free concept, abrasion effects are more brilliant than the conventional method. Yarns were found clean, and overall, It achieved more satisfaction from the quality team in implemented factory.
Process time: with Soko stone-free concept 15 minutes less time is required per batch.
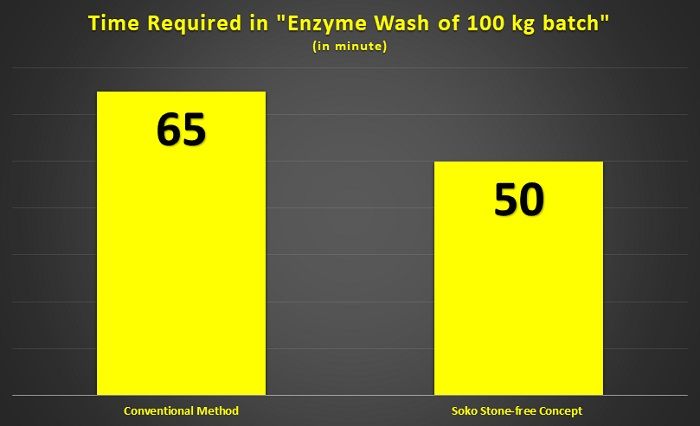
Fabric strength: Since stone weakens the fabric strength, garments washed in the conventional method carry the risk of wear and tear. On the other hand proposed method uses only half the amount of stones compared to the traditional way and is completely safe in terms of fabric strength.
Stone usage: Bioclean works as an abrasion booster, and 62 kg stone is less used in 100 kg batch than the conventional method. Here, the stone saving percentage is 50%.
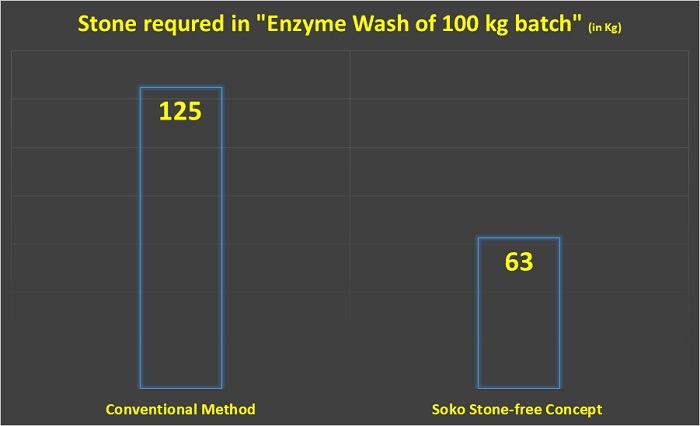
Energy consumption: Since the proposed method requires 15 minutes less machine run time than conventional and Bioclean is applied at room temperature, less energy is consumed in the proposed way.
Associated chemical cost: Since we mentioned the key differentiating segments of the conventional process and proposed process above, we have calculated the associated chemical cost and found that BDT 700 can be saved per batch (100kg). Details are as bellows-
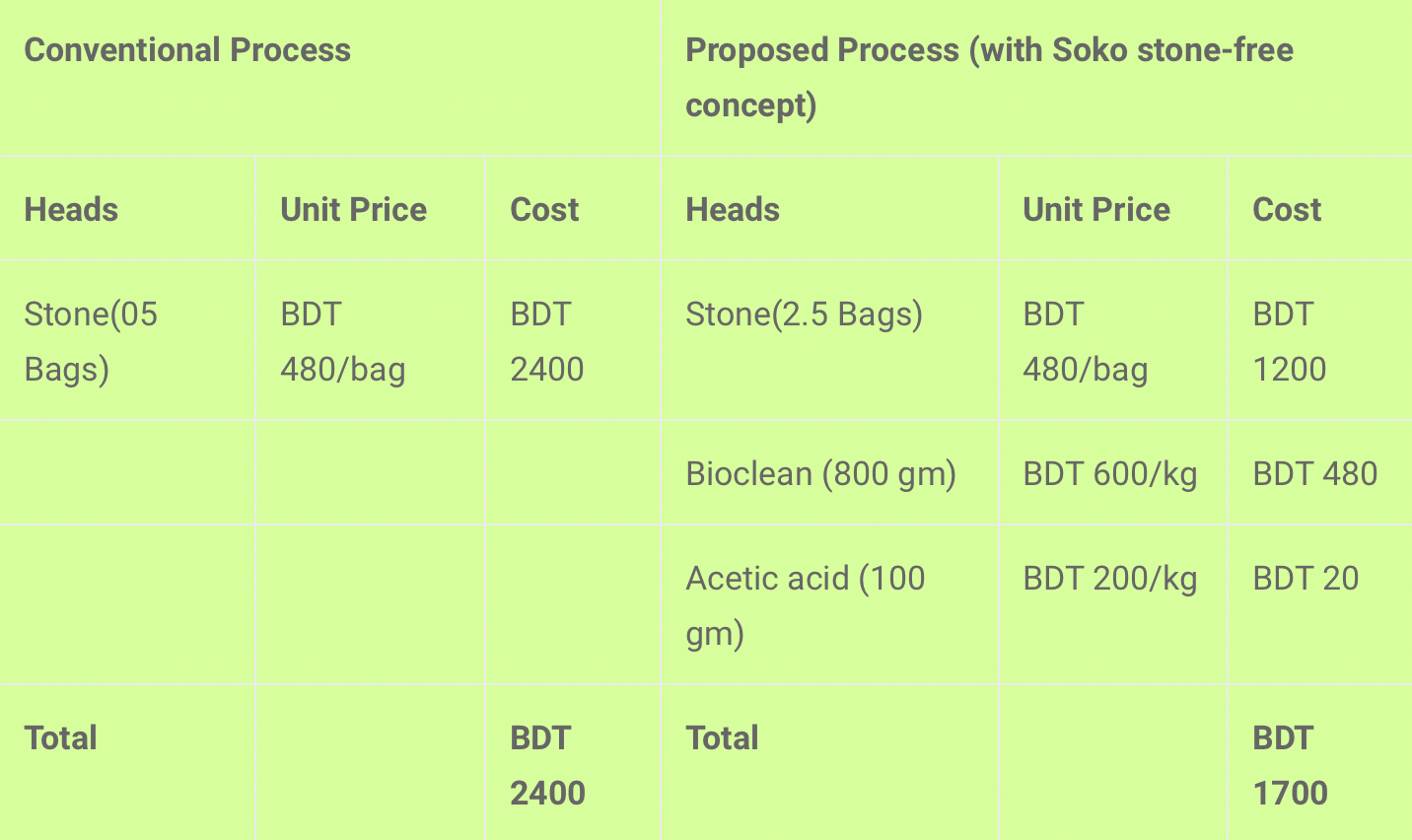
*Acetic acid price is abnormal due to the market crisis
*Prices are taken on 20th March. It may vary due to the market situation
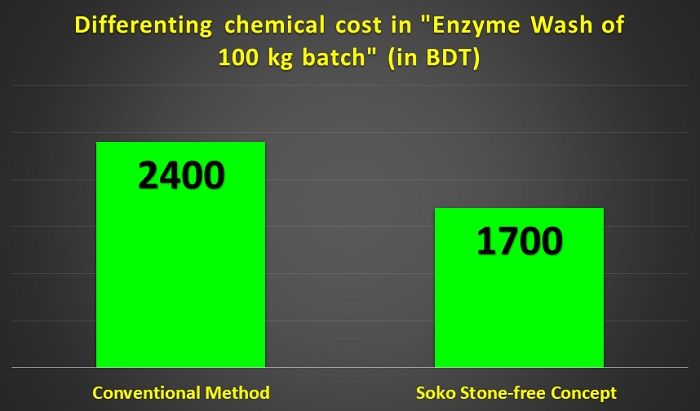
Perfect cleaning: Pocket bag’s color of the proposed washing method showed a significant difference from the conventional washing method. No back staining was noticed in the proposed washing method, and it was perfectly clean.

Less sludge: Less sludge is produced from the proposed washing method since 50% stone is less used. Less treatment cost is required for fewer stones.
Less permanganate: Since Bioclean makes scrapping area’s whiteness more visible, so less permanganate is required. Using less permanganate improves health and safety of workers and contributes to environment sustainability.
Analyzing the project result, summary of the overall benefits are:
- More contrast
- Reduce the stone-wash process time
- Reduce the loss of fabric strength due to long stone-wash process
- Reduce the use of stones
- Reduce energy consumption
- Reduce overall cost
- Perfect cleaning of white yarn and pocket linings
- Reduce the use of Permanganate
- Improve the crocking fastness
- Nice grey cast
- Low temperature
- Replace ozone treatment, reduce the long procedures and manual operations
- Produce less sludge
Bioclean Soko is only applicable for indigo denim. And for indigo denim, stone is still required in the proposed method, and Soko is working on it relentlessly to make it better in all terms.