Mohammad Shadekul Islam (Industrial Expert), Product Engineer at IKEA supply AG
K.M Kashiful Hasan Sisir (Industry Supervisor), DGM (Yarn Manufacturing), Mosharaf Composite Textile Mill
Md. Numan Bin Faruqe (Industry Supervisor), Senior Executive (Lab & QC department), Zaber & Zubair Fabrics Ltd.
Abstract
The properties of sustainable melange yarn which is made from jute and cotton through the blending process were investigated. To reduce the environmental impact of using synthetic fiber, dependency on cotton fiber.
Cotton is reduced 30% by using jute through the blending process and ration of cotton: jute (70:30). The properties are developed through a good opening of jute fiber, chemical processing and changing some machine parameters.
The properties of Jute cotton blend melange yarns are compared to usual rotor yarn. 10Ne, 12 Ne, 16 Ne counts jute cotton blended melange yarn are compared with regular 10 Ne, 12 Ne, 16 Ne rotor yarn. The processed jute fiber length is 35 -40 mm and the cotton fiber length is 30-35 mm. Used jute fiber is 100% tossa, origin Bangladesh and cotton fiber code is DCH-32, origin India.
Jute fiber is dyed with a reactive dye for developing the melange effect. The yarn is produced by the Rotor spinning system. Three count 10 Ne, 12 Ne and 16 Ne yarn are produced in the Rotor spinning process and compared to the usual rotor spinning yarn. These three count yarn U % are 16.14, 13.03, 14.36, IPI are 5470, 1363, 3882.5, c are 7.68, 4.16, 4.29, CSP are 1313, 1806, 1642, Elongations are 5.18 %, 4.21 %, 5.08 %, Tenacity are 12.476 cN/tex, 12.18 cN/tex, 12.44 cN/tex.
After analyzing the properties, it is found that the Hairiness of the melange yarn is less than 100% cotton rotor yarn which is good. Also the melange yarn U %, Tenacity (cN/tex) and CSP are relatively close to 100% cotton rotor yarn. But IPI is very not good to compare to the 100% cotton rotor yarn.
Keywords: sustainable, environmental, the opening of jute fiber, machine parameter, melange, rotor yarn, counts, tossa, DCH-32, reactive dye, U %, IPI, CSP, Elongations, Tenacity.
Introduction
Jute fiber, flax fiber, hemp fiber are bast fiber which obtained from their plant. Bangladesh produces 5.5-6 million bales of raw jute every year. On the other hand, Flax fiber is very costly and imported every year. The chemical compound namely cellulose (58~63%), hemi-cellulose (20~24%) and lignin (12~15%), and some other small quantities of constituents like fats, pectin, aqueous extract. Nowadays, in the jute sector, the demand for diversified jute uses and improved quality is increasing for the use in different areas home textile example curtain, floor covering, sofa cover are so on.
Cotton is considered “The King” of all fibers. Rising global demand for this fiber has led to the manufacture of synthetic fibers which are neither eco-friendly nor completely biodegradable. Hence, for a long time, researchers have been looking for natural replacements for synthetic fibers, which are easily available, green, and renewable, and at the same time sustainable resources.
Blending is a technique to overcome the poor characteristics of one fiber. It is the technique to combine fibers that emphasizes the good qualities and minimizes the poor qualities of the fibers. It also makes the fabric manufacturing process economical. Jute-cotton blended yarn is one of the examples of it [1]. Blending jute with cotton fiber may be an acceptable way of jute diversification by which value-added products can be produced. Jute fibers have several advantages like a lustrous golden appearance, high tenacity and good properties.
In our project work we observed the various yarn properties like U%., CV%, Imperfection Index (thick/km, thin/km, neps/km), hairiness and strength (CSP) of jute cotton blend yarn (30:70) 10 Ne, 12 Ne and 16 Ne rotor yarn with 100% cotton 10 Ne, 12 Ne and 16 Ne rotor Yarn and develop jute cotton melange yarn by jute part dyeing.
Blending is a long-practiced method and being diversified depending on expanding demand of local and global markets of apparel, home textiles and technical textiles. Jute-Cotton blend is one of the possible options to reduce the dependability of cotton. Reported blending jute with cotton fiber is an acceptable way of jute diversification by which value-added products can be produced [7]. Natural jute as a textile fiber suffers from inherent defects which limit its spinning to yarn for producing packing clothes.
The blending of fibers is usually made with different fibers having dissimilarity in their properties, to achieve or improve certain characters of the yarn or its processing performances. Fabric produced from the blended yarn might have better characteristics than what could be obtained in a fabric produced from a single fiber. Any successful attempt to blend this fiber with cotton would be a breakthrough in the field of textile.
The most important property of textile fiber is the spinning property. Due to the inherent defects of jute, its spinning properties are not good. With the very expectation of success in fine spinning, it would be interesting to develop fiber spinning technology for versatile textile use of jute fiber. Again, the spinning of more fine yarns from jute cotton blends has not been possible without woolenization and machine setup of cotton carding. With the increase in the level of concern about the environment and the price of petroleum, people are paying more attention to jute and its products, especially for textile applications.
However, as jute also has a few undesirable properties such as stiffness, harshness, and low extensibility after the chemical degumming process [8], cotton and jute fibers are blended and spun into blended yarn. The strength of the spun yarn is recognized as one of the most important quality parameters of yarn [9]. Several past studies indicate that the effects of gauge length on tensile properties of the ring, open-end, friction and air-jet yarn are different, [10][11].
Jute fiber conventionally is not used for producing wearable textile products as it has some shortcomings regarding feel, stiffness, drape, coarseness, washability and abrasion. Jute as a ligno-cellulosic bast fiber, which possesses hard and harsh qualities also makes it difficult to produce apparel and other fancy fabrics to use in our day-to-day life. It is so stiffer fiber which limits its textile application. For the stiffness of this fiber, it is also not spinnable like other fibers. BJRI develops jute/cotton blend yarn which is called “JUTTON” but their yarn properties like U%, Strength and Hairiness are not good enough to produce good quality fabric[12].
Experimental Section
Materials
Opened and processed jute fiber of 45-50 mm staple length was dyed to blend with cotton 30-35 mm at some certain ratio to preparing jute cotton melange yarn. Pretreatment process was done in Janata jute mills ltd. Na2S2O4, NaOH, castor-oil-emulsion, H2O2, Dish soap, HCL, Reactive dye and Ultratex® SI are used for pretreatment with the dyeing of jute fiber.
During 1st trail 150 gm processed jute fiber and 350 gm cotton fiber was used to maintain 30:70 blending ratio. During 2nd trail 50 kg processed jute fiber and 200 kg cotton fiber was used to maintain 30: 70 blending ratio. Jute was collected from Janata jute mills ltd and cotton was provided by the Noman group (spinning section). The spinning was done through rotor spinning process in the Zaber Spinning mills of the Noman group. Measuring balance, Jute opening machine, softening machine, chemical processing machine and all required chemicals are available in Janata jute mills ltd.
Jute fiber preparation
Jute cotton melange yarn was made from processed dyed jute fiber by blending with cotton fiber. Raw jute fiber is very rigid and inapt for cotton spinning. It needs to increase spin ability by improving flexibility. To improve the flexibility of jute fiber was treated mechanical and chemical processes. In the mechanical stage, jute fiber was opened by jute breaker card machine and finisher card machine which is called the double opening process. Before carding 2% castor oil emulsion was used to soften the jute fiber.
In chemical processing 1st stage De-coloration process opened jute fiber were treated by 3 ml/L Na2S2O4, 4 ml/L NaOH, 1 ml/L Dish soap at 110 for 40 min and washed by 1 ml/L HCL and 2ndstage Oxidation process was done by 7ml/L H2O2 (50%), 2 gm/L NaOH, 1gm/L Detergent at 110 during 50 min and neutralized by 1% acetic acid. After pretreatment jute fiber was dyed by Reactive dye (light blue color). After dyeing, jute fiber was soften by using Ultratex® SI.
Yarn preparation
Finished dyed and non-dyed jute fibers were used to blend with cotton fiber with some ratio jute: cotton 30:70 before mixing dyed jute fiber was opened through Roving opening machine. Dyed jute fiber and cotton fiber was blended by a multi-mixture machine at the blow room section of Zaber Spinning Mills.
After blending carded sliver was made and drawn the carded sliver to maintain count 0.11 Ne. finished drawn sliver directly used in rotor spinning and made rotor yarn. Three types count rotor yarn was produced.

Step by step process of jute cotton melange yarn production
- Jute Fiber opening: Jute fiber was opened by Double carding process. In double carding process Breaker card and finisher card machine was used. For fine and smooth opening 2% castor oil was used with 1.5% emulsifier by spreader machine before jute carding. After emulsification jute fiber was delivered to carding section for opening. The delivery speed of jute breaker card was 700 lb. /hr. and finisher card was 400 lb. /hr. The sliver count was 19.5 lb. /100yd.
- Chemical Treatment process: De-coloration process opened jute fiber were treated by 3 ml/L Na2S2O4, 4 ml/L NaOH, 1 ml/L Dish soap at 110 during 40 min and washed by 1 ml/L HCL and 2nd stage Oxidation process was done by 7ml/L H2O2 (50%), 2 gm/L NaOH, 1gm/L Detergent at 110 during 50 min and neutralized by 1% acetic acid. In this bleaching process by 1:4 liquor ratio.
- Fiber Dyeing and softening: After pretreatment jute fiber was dyed by Reactive dye where shade % 1.5. Glubar salt 40 g/l, NaOH 0.5 g/l, Wetting agent 1 g/l are used to dye the jute fiber. The dye process is done within 1 hour and maintains a temperature of 60˚C. After dyeing, jute fiber was softened by using Ultratex® SI and the amount is 1.5 g/l. In this dyeing and softening process liquor ratio of 1:6 is used.
- Blending of Jute-cotton fiber: For production unimix machine was used in Zaber Spinning. The blended ratio was 30: 70 (jute: cotton). The compact mixing machines UNImix B 72 is fed from the pre-cleaner. The material is evenly distributed across eight mixing chambers.
- Carding: Card web was produced from a carding machine. Carding machine ensures uniform fiber alignment. After uniform mixing fiber was transmitted to Carding machine which designated DFK, type-no. 5490701, manufacturing year 2000, Trützschler GmbH & co. The delivery sliver count was 0.11 Ne.
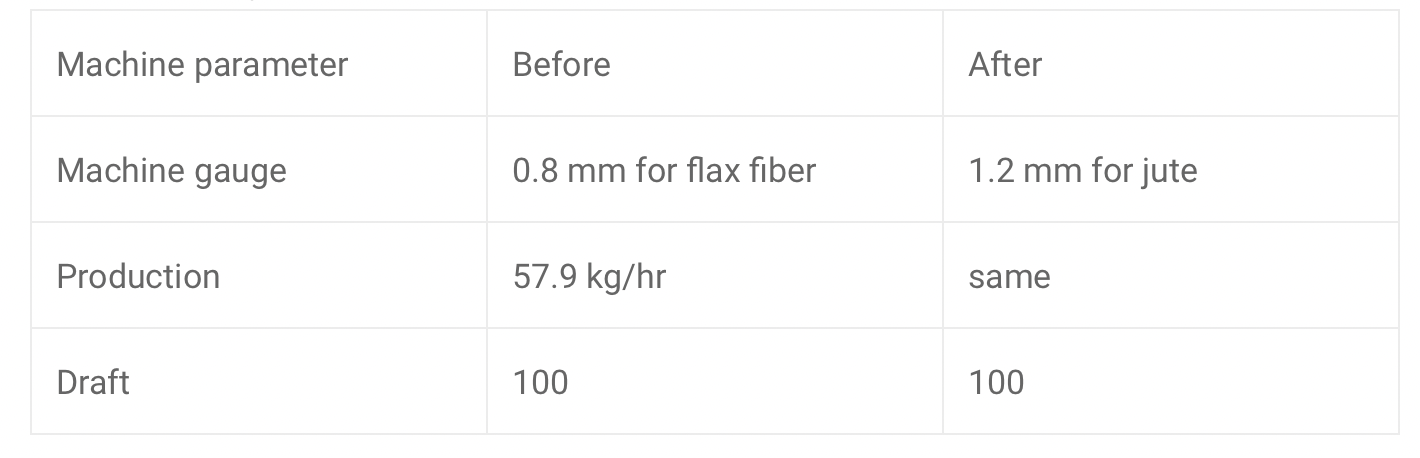
6.Doubling and Drawing: For uniform sliver and to make good quality yarn in rotor spinning doubling and drawing is an important process in spinning. Doubling and drawing was done in the breaker draw-frame and finisher draw-frame machine. Produced 0.11Ne count finished drawn sliver by maintaining draft. Finisher draw-frame machine origin, brand name, serial no. Company names are Japan, DX7AH, FDS0198, Marubeni TEXMATEX Corporation. Finisher draw-frame machine origin, brand name, Brand name are Germany, RSB-D30, REITER.
7.Rotor spinning: Finally, jute cotton blend mélange was produced in Rotor spinning. The input of the rotor spinning machine was finished drawn sliver which count is 0.11 Ne. 10 Ne, 12 Ne and 16 Ne count were produced. Rotor speed was 1.08 lack rpm. The Rotor machine origin, brand name, serial no are Switzerland, Oerlikon Schlafhorst, autocore 8.
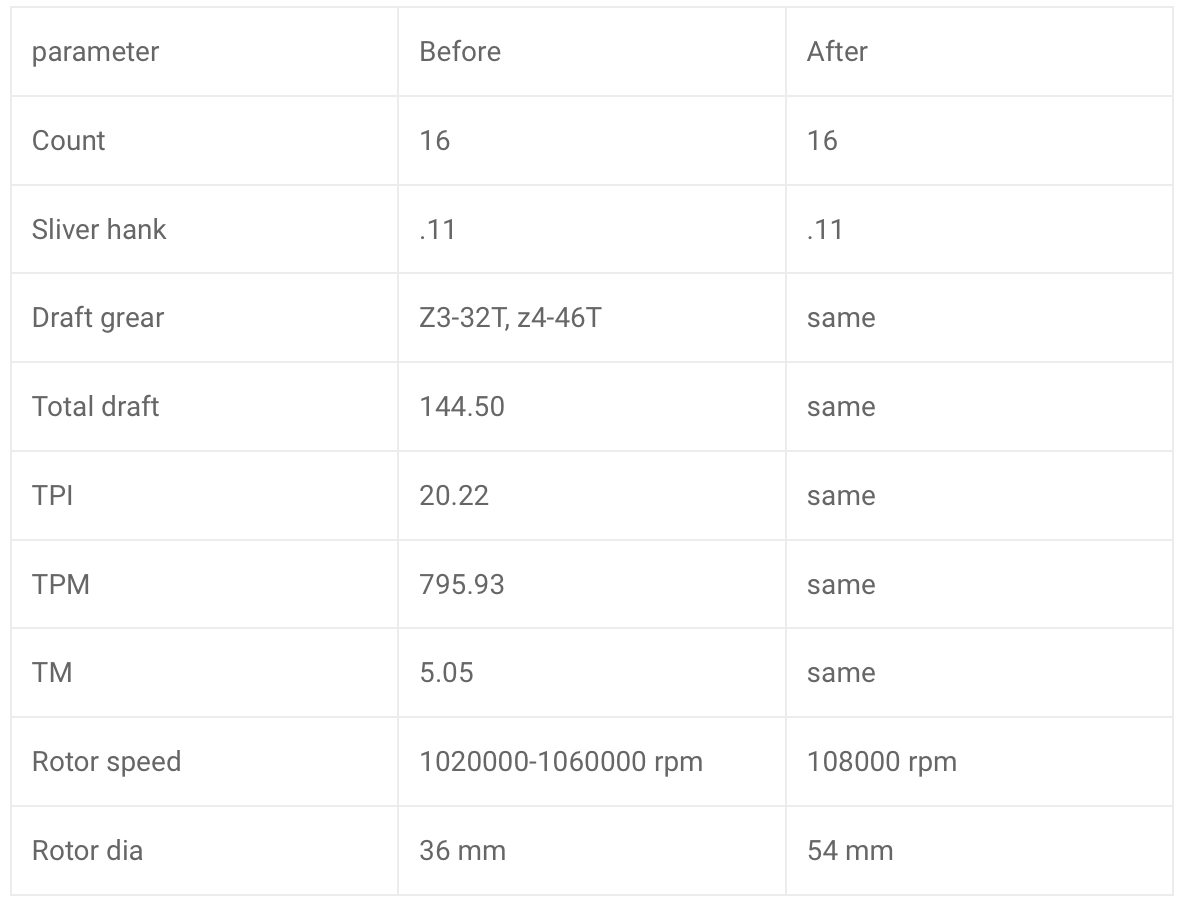

Characterization Techniques
Cut Jute fiber, cotton fiber and jute cotton blend fiber length is measured by the Fiber sorter method/ array method. A comb sorter machine is used for pretreated jute fiber, raw cotton and blended jute cotton fiber length analyses. Single yarn strength, Unevenness (U %), Imperfection Index (IPI), Thick place, Thin place, Neps, Hairiness (H), like Micronaire, Length, and Strength are tested of the melange rotor yarn and 100% cotton rotor yarn. MesdanLab Strength Tester machine is used to do a single rotor yarn strength test of jute cotton blend melange yarn which blending ratio is 70:30 (cotton: Jute).
Sample length was 500 mm and clamped speed 500 mm/min. Yarn properties like Unevenness (U %), Imperfection Index (IPI-Thick place, Thin place, Neps, Hairiness (H). Yarn properties indicate yarn quality. That important parameter of yarn properties is tested by USTER® TESTER 5 – S800 testing machine. Sliver hank is determined by using Warp block of 1-yard circumference, AS 220.R2 PLUS Analytical Balance for sample weight measuring which maximum capacity (MAX): 220g and Readability: 0,1 mg.
Testing machine and Equipment
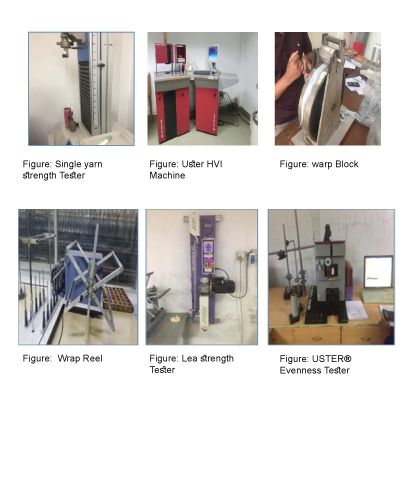
Results and Discussion
After the blending process of jute and cotton fibers, card sliver is tested, micronaire, strength and length are also tested. Jute cotton blend melange yarn is characterized by a different parameters such as single yarn strength, Imperfection Index, Hairiness, Unevenness.
Comb sorter diagram
Jute fiber

Jute cotton blend Fiber:

Properties analyses of Blend fiber
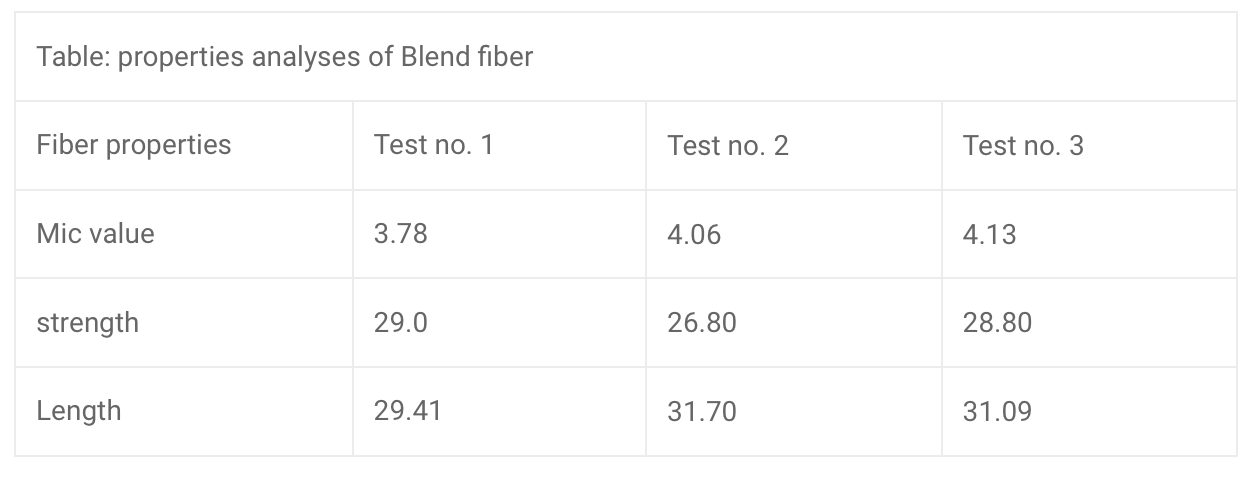

The Mic value range of cotton fiber in ring spinning is 3-6. So jute cotton blend fiber average fineness (Mic) is 3.99 which is good for spinning in rotor process.

The fiber length range of cotton fiber in ring spinning is 10-65 mm. Therefore, jute cotton blend fiber average length (mm) is 30.73 mm, which is good for spinning in the rotor process.

The fiber strength range of cotton fiber in ring spinning is 24-32 gm/tex. So jute cotton blend fiber average strength (gm/tex) is 28.2 gm/tex which is good for spinning in the rotor process.
Yarn properties analyses
Jute cotton blend melange yarn is characterized by a different parameters such as single yarn strength, Imperfection Index, Hairiness, Unevenness, Elongation %. CSP. Here three count yarn parameters has shown in the table.
10 Ne, 12 Ne, 16 Ne jute cotton blend yarn (30/j: 70/c) properties compared with 10 Ne, 12 Ne, 16 Ne of 100% cotton rotor yarn.
Tested yarn properties data are given below:

Comparison of mass variation:
U% and CV%: These are the mass variation calculations along yarn length. Testing machine measures the mass of each centimeter of yarn and U% and CV% values are calculated using the following formula and these are worldly used to determine how uniform or even the yarn is.
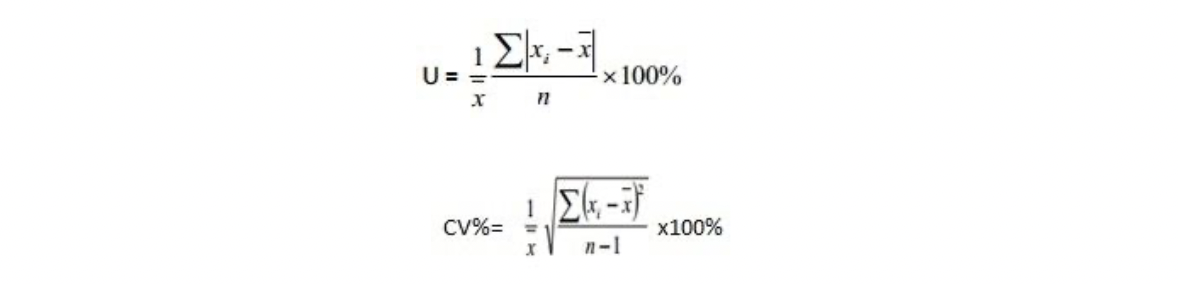

From this analysis, the mass variation of 16 Ne mélange yarn is 26% greater than 100% cotton rotor yarn. And the mass variation of 12 Ne and 10 Ne mélange yarn is also 28% and 35% greater than 100% cotton rotor yarn.
Comparison of imperfection
IPI of blend rotor yarn is very bad compared to non-blend rotor yarn. The yarn delivered from the rotor frame is passed through the measuring slot of the USTER evenness tester, which works on the principle of capacitance.
Finally, the results arrived from the tester are unevenness % and imperfections. Generally thin (-40%) to (-50%), thick (+50%) to (+70%) and neps (+140%), (+200%) & (+280%) are taken into consideration for rotor spun yarn. The testing speed is for 400 mpm and testing time is 1 min for each test. 5 single test is done and considers the mean value.

We know that the more IPI value means the bad quality of yarn. From this analysis, the IPI of 10 Ne mélange yarn is much more than 100% cotton rotor yarn. And the IPI of 16 Ne mélange yarn is also greater than 100% cotton rotor yarn. But the IPI value of 12 Ne mélange yarn is relatively close to the IPI value of 12 Ne 100% cotton rotor yarn. The IPI of the mélange yarn is bad because jute fiber is thicker than cotton fiber and also for changing the machine gauge of the carding machine.
Comparison of hairiness
Rotor yarn shows the least hairiness whereas the hairiness of rotor spun yarn is lower than ring-spun yarn. The hairiness of these yarn are tested by USTER® TESTER 5 – S800 testing machine on the optical principle. The image of the protruding fibers from the surface of the yarn are captured and sensed by an array of detectors. Then it is accounted in a corresponding segment to get the values with the range of 1 to 12mm.
Generally, the S3 value (total number of protruding hairs above 3mm length) is taken into consideration for hairiness measurement. The blend rotor yarn hairiness less than 100% cotton rotor yarn.

We know that less hairiness value means good quality of yarn. From this analysis, the hairiness of 10 Ne mélange yarn is 4% less than 100% cotton rotor yarn. And the hairiness of 16 Ne mélange yarn is also 12% less than 100% cotton rotor yarn. The hairiness value of 12 Ne mélange yarn is 6% less than 100% cotton rotor yarn.
Comparison of strength (CSP)
CSP is the result of Count Product strength. The Strength indicates lea strength of the yarn. A lea strength tester measures the strength of one lea yarn. One lea means 120 yds. When the sample is torn out the m/c is stopped and the reading is taken.

We know that more CSP means good quality of yarn. From this analysis, the CSP of 10 Ne mélange yarn is much less than 100% cotton rotor yarn. And the CSP of 16 Ne mélange yarn is relatively close to 100% cotton rotor yarn. But the CSP of 12 Ne mélange yarn is also less than 100% cotton rotor yarn.
Comparison of single yarn strength (Tenacity)
The Tensile Strength expressed as force per unit linear density is called tenacity. This is normally expressed as centi-newton per tex (cN/tex) or gram force per tex (gf/tex). The higher the value, the better the strength of the yarn. In the case of blend yarn of 12 Ne count show better strength than 100% cotton rotor yarn.

From this analysis, the single yarn tenacity of 10 Ne mélange yarn is 15.5% less 100% cotton rotor yarn. And the single yarn tenacity of 16 Ne mélange yarn is 10% less than 100% cotton rotor yarn. But the tenacity of 12 Ne mélange yarn is 5.4% greater than 100% cotton rotor yarn.
Yarn Elongation
It is the measure of the extent of deformation along the axis of a material under tensile stress expressed as a percentage change in length based on the original length of the Test Sample. The percentage of length up to which the yarn can be extended before the occurrence of yarn breakage.

From this analysis, the single yarn elongation of 10 Ne mélange yarn and 100% cotton rotor yarn is 3.572% and 11.982%. The elongation of 12 Ne mélange yarn and 100% cotton rotor yarn is 5.08% and 9.65%. The elongation of 16 Ne mélange yarn and 100% cotton rotor yarn is 4.21% and 8.97%.
Cost analysis:
Cotton price ( high quality): 176 tk/kg)
Total wastage of 100% cotton rotor yarn production: 11%
Sources: Dhaka Cotton, Green fibers, Zed cot, Prime, Fibers, etc.
For melange yarn
Jute fiber total cost: 120 tk/kg
Total wastage- 16% of melange yarn production.
Cost reduce: 5.5%
Conclusion
Jute and cotton both are natural fibers. Reduce using cotton fiber, flax fiber and increase using jute fiber which is produced in our country. Jute fiber is a sustainable fiber. We know Jute as a golden fiber. Bangladesh produces 5.5-6 million bales of raw jute every year. On the other hand, Flax fiber is very costly and imported every year. Developed melange effect by dyeing the jute fiber of jute/cotton blend yarn.
This will be the alternative of flax-cotton melange. Different types are produced from this jute cotton blend yarn. Home textile is the main concern application of the fabric. To produce melange yarn blended with jute/cotton is a good scope that has not been done yet.
Also developed the properties of the blended yarn like strength, hairiness, U%. SEM images captured of jute cotton blend card sliver to visualize the morphology of the fiber.
3 view is captured, A. 20 B. 10 C. 3 . The morphological view of fiber can be viewed from this SEM test. Comparatively, thick fiber is the bleached jute fiber and comparatively, thin fiber is the cotton fiber. 12 Ne, 16 Ne jute cotton blend yarn (30/j: 70/c) properties compared with 10 Ne, 12 Ne, 16 Ne of 100% cotton rotor yarn. CVm percentage of 16 Ne, 12 Ne, 10 Ne Melange yarn is 26%, 28%, 35% greater than 100% cotton rotor yarn. Less hairiness means good quality of yarn.
The Hairiness of 16 Ne, 12 Ne, 10 Ne Melange yarn is 12%, 6%, 4% less than 100% cotton rotor yarn. In addition, the Strength of Melange yarn is comparatively better than 100% cotton rotor yarn. However, the Elongation of Melange yarn is comparatively worse.