Sayed Iqbal Rizvi (Industry Expert), Managing Director, Sameet Dyes & Chemical
Md. Rashedul Islam (Industry Supervisor), Gm (Knitting & Dyeing), Aps Group
Kazi Sirajul Islam (Academic Supervisor), Lecturer, Dept. of DCE, Bangladesh University of Textiles
Abstract
The textile dyeing sector is one of the most environmentally polluting sectors in Bangladesh. The conventional dyeing method includes using a huge amount of water, salt, soda, and other chemicals. Due to the hydrolysis of reactive dye, a huge amount (almost 30 to 40 percent) of the dye remains unfixed in the dye-bath.
All the chemicals and unfixed dye make the wastewater more complex to treat in ETP (Effluent Treatment Plant).

All the textile factories are looking for a sustainable and cost-effective dyeing method for surviving in the upcoming fourth industrial revolution, where sustainability will be the top priority. Cationic cotton dyeing is a dyeing method where it removes the necessity of salt, reduces the water, chemicals, auxiliaries’ use.
The cationization process eliminates the hydrolysis of dye and reduces the necessity of wash-offs. In this research work, the viability and feasibility of cationic cotton dyeing for the industrial and commercial-stage were tested in terms of quality, quantity, and cost.
The treatment of cationization with the chemical CHPTAC (3-chloro-2-hydroxypropyl trimethylammonium chloride) was performed at different concentrations. The color strength was measured after completing the dyeing process, which was 5% to 25% better compared to conventional dyeing.
The colorfastness properties were measured, which was improved compared to conventional dyeing. The bursting strength of the fabric was tested to check the impact of cationization on strength.
For measuring the environmental impact, BOD, COD, TDS, DO, PH of effluent was tested, which was significantly improved. Finally, the cost of cationic cotton was calculated, which was challenging for commercial application.
Keywords: Cationization, color strength, colorfastness, sustainability
Introduction
The reactive dye is most commonly used for dyeing cellulose fiber (cotton) because of its wide range of use, better color yield, and good fastness properties. The reactive dye is anionic in nature (Lewis DM, 2007) (D.P. Chattopadhyay, 2007), while the cellulose fiber comes in contact with water, it produces a small negative charge as the hydroxyl group presents in the cellulose structure get ionized. (Lewis DM, 2007) (D.P. Chattopadhyay, 2007).
During the dyeing process, the same charge of the material (cotton fabric) and reactive dye result in repulsion which ultimately introduces the necessity of electrolyte (Glauber’s salt or common salt) to continue the process (Broadbent, 2001).
When the electrolyte is used for the dyeing process 30 to 40 percent dye is hydrolyzed, which reduces the efficiency of the process. The electrolyte used in the dye-bath remains unchanged after the dyeing process.
At the same time for the fixation of reactive dye alkali (soda ash) is required. All the chemicals, hydrolyzed dye make the wastewater more complex to treat in ETP (Effluent treatment plant) and increase the cost of the process (Burkinshaw, 2002) (Burkinshaw R. S., 2003).
Conventional dyeing is less efficient due to the hydrolysis of dye, poor exhaustion, and the necessity of more wash offs (D.P. Chattopadhyay, 2007).
To reduce the problem, the material (cotton fabric) or the reactive dye needs to be different like the charge (anionic/cationic)
Cationization is the process where cellulose polymer reacts with a different type of substituted amino compounds, to impart positive sites in the polymer structure. By this process, the cotton fiber becomes cationic from anionic nature.
As a result, the cotton can easily create an ionic bond with the anionic dye (reactive dye) (Tabba, 2006) (M. Montazer, 2007).
The introduction of positive sites in the cotton structure eliminates the necessity of electrolyte, improves the dye exhaustion percent, reduces the number of wash-offs (Fraze, 2002) (M. Subramanian Senthil Kannan, 2006).
In this research work, CHPTAC (3-chloro-2-hydroxypropyl trimethylammonium chloride) was used for the cationization process at different concentrations. CHPTAC is most popular for cationization because of improved dye exhaustion, better color yield, and more environmentally friendly (Mohamed Hashem, 2003) (Mehmet Kanik, 2004).
Lili Wang et al. (2009) concluded that higher dye utilization and better color yield have been found on the cationic cotton than the conventional one. Researchers also found better levelness of dyeing and good fastness properties on cationic cotton dyeing. Sanjit Acharya et al. (2014) observed that color strength (K/S) after completing dyeing is significantly higher than conventional dyeing for reactive dye. The researcher observed that dye exhaustion increased while treating the fabric with the CHPTAC due to an increase in the cationic sites that ultimately gives a better color yield. Nallathambi A., Venkateshwarapuram (2018) has been described that the total dissolved solids (TDS) value were four-time lower than the conventional process in the wastewater. Nebojsa Ristic and Ivanka Ristic (2012) concluded that fabrics treated with cationic reagent, have more positive zeta potential compared to the untreated fabric which has a favorable influence on reactive dye. The researcher also found that color intensity reached its maximum while the fabric is cationized. Although a large number of research project and study has been conducted about cationization and salt-free dyeing, the viability and feasibility check in terms of quality, quantity, and cost for the industrial and commercial stage are very limited.
To check the viability and feasibility of the commercial approach, the color strength, colorfastness, bursting strength, and effluent quality were tested and compared with the conventional dyeing. The processing cost was also compared with conventional dyeing.
Materials and methods
Fabric
100% cotton knit Single Jersey with GSM 160 was used. The yarn count was 26s and the stitch length was 2.9 mm
Chemicals
The cationization chemical CHPTAC (3-chloro-2-hydroxypropyl trimethylammonium chloride) was collected directly from Dow Chemical Bangladesh Private Limited. This chemical is commercially available in the name of ‘CR 2000’, which is a 65% aqueous solution of 3-chloro-2-hydroxypropyl trimethylammonium chloride. Sodium hydroxide (NaOH) was used as a catalyst for CHPTAC in the cationization process.
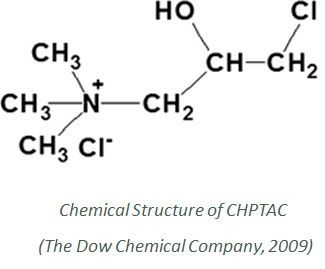
Other chemicals include wetting agent, sequestering agent, sodium hydroxide, hydrogen peroxide, stabilizer, peroxide killer, sodium sulfate (Na2SO4), sodium carbonate (Na2CO3), Bio polishing enzyme (Enzymel-2500), acetic acid, a leveling agent of commercial-grade were also used. Reactive Dye from Novacorn was also used throughout the project.
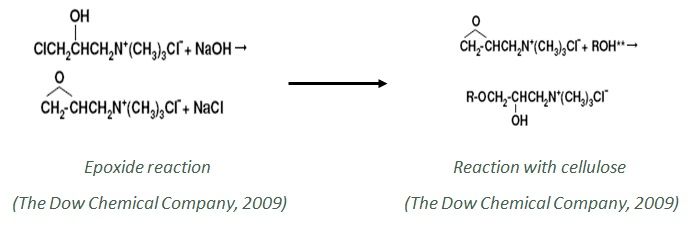
Pre-treatment of fabric
Scouring and bleaching:
The fabric was scoured and bleached at the same time with the below recipe
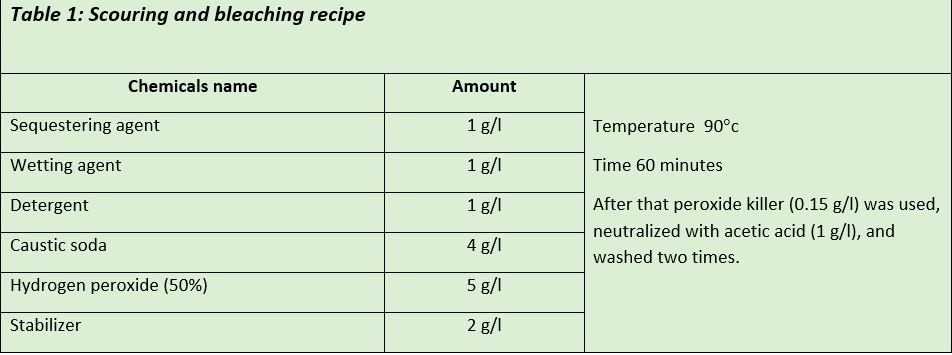
After scouring and bleaching the Bio polishing enzyme (Enzymel-2500) was used at 0.25 g/l. The process was continued for 60 minutes at 55°c temperature in an acidic medium (PH 5.5). After that temperature was raised to 75°c to kill the enzyme.
Conventional dyeing
The pre-treated fabric was dyed for different shade percentages at 60°c temperature with a wetting agent 1 g/l, sequestering agent 1 g/l. The amount of salt and soda is measured according to shade percentage. The fabric was normally washed, hot washed and rinsed. (See table 3)
Cationic cotton dyeing
The pre-treated fabric was first cationized using CHPTAC at different concentrations. Caustic soda was used according to the concentration of CHPTAC. The fabric was immersed in the solution of 1 g/l wetting agent, CHPTAC, and Caustic soda.
The temperature was raised to 90°c and run for 25 minutes. Then the bath drained and checked the PH. 0.5 g/l acetic acid was used if the PH was more than 7.5.
For dyeing cationic cotton, 1 g/l leveling agent, 0.5 g/l sequestering agents, 1 g/l wetting agent was used. Then the dye was dosed and run for 60 minutes. After that soda was dosed and run for 60 minutes. After that bath was drained and hot-washed fabric. (See table 3)
Measurement of color strength (K/S)
The value of color strength was directly collected from Datacolor 650 Spectrophotometer. The build-in software in a computerized color matching system gives the k/s value in all visual spectrums. The comparison of shade (darker/lighter) was also found from the device.
The reflectance (R) value of dyed fabric at the maximum wavelength of absorbency (l max) was found and color strength was calculated through the Kubelka Munk equation.
The Kubelka Munk equation…
Where R is the reflectance, K is absorbance, and S is the scattering.
Testing – Methods – Instruments
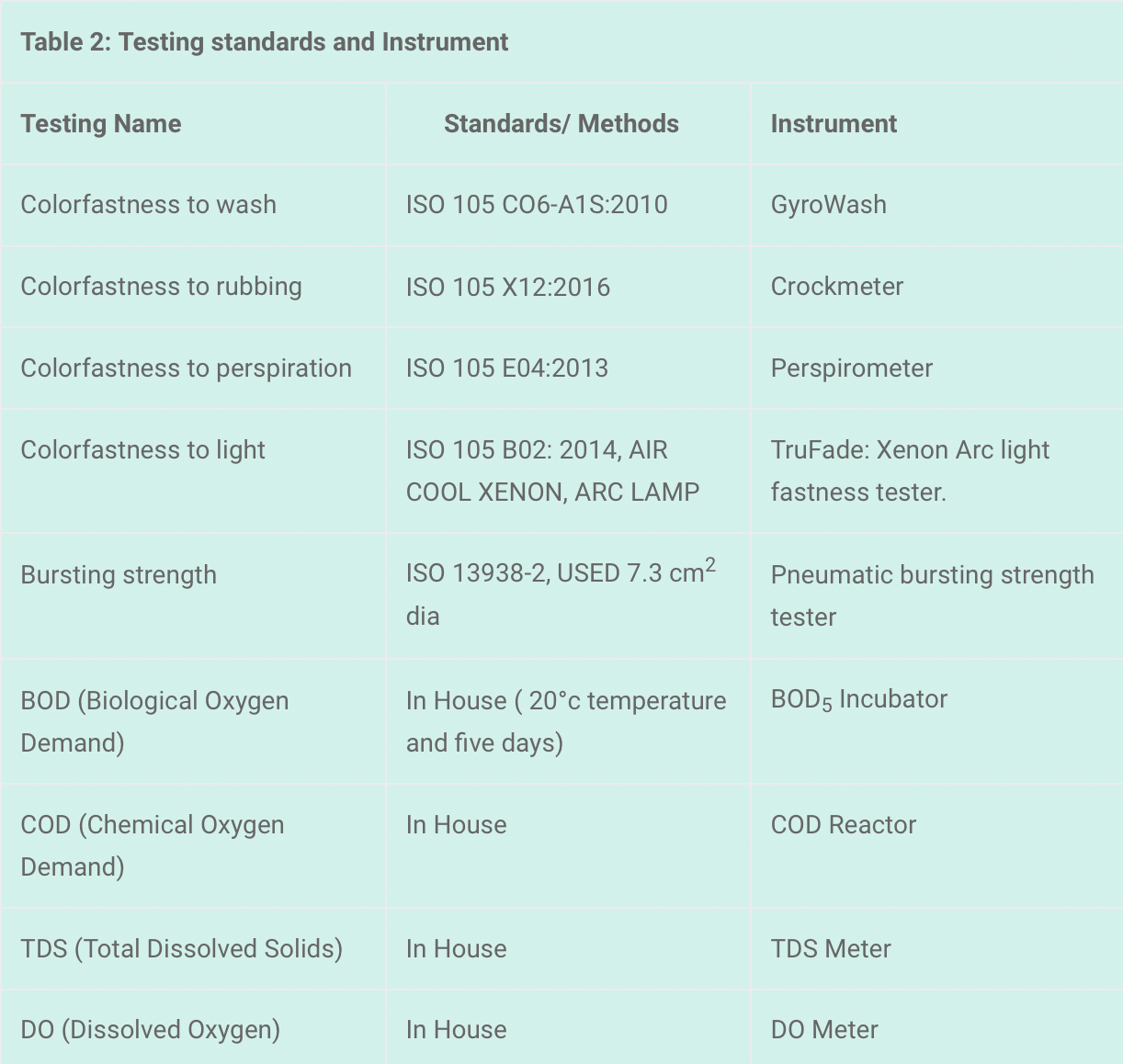
The PH of the effluent was measured through a digital PH meter.
Results and discussions
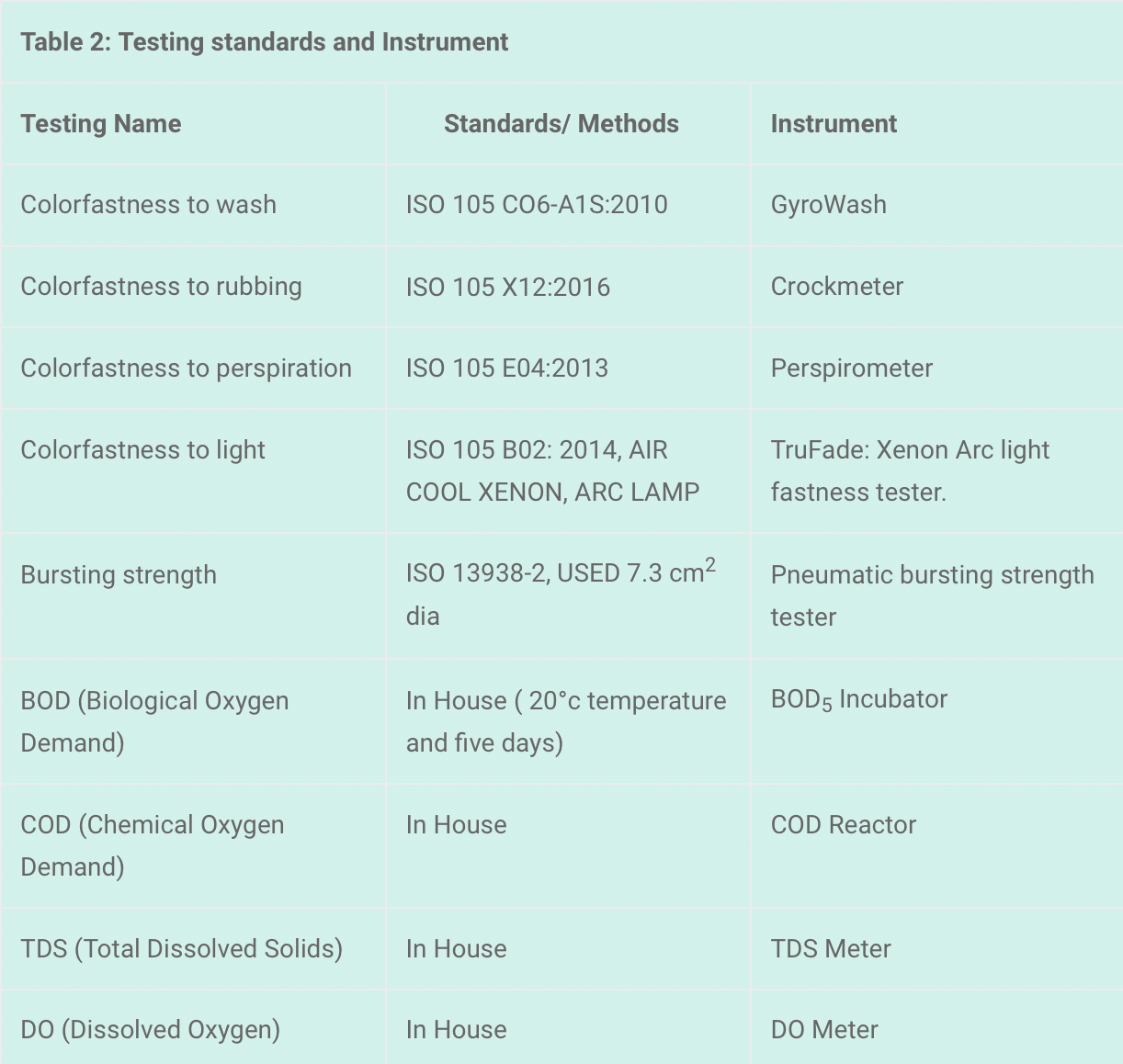
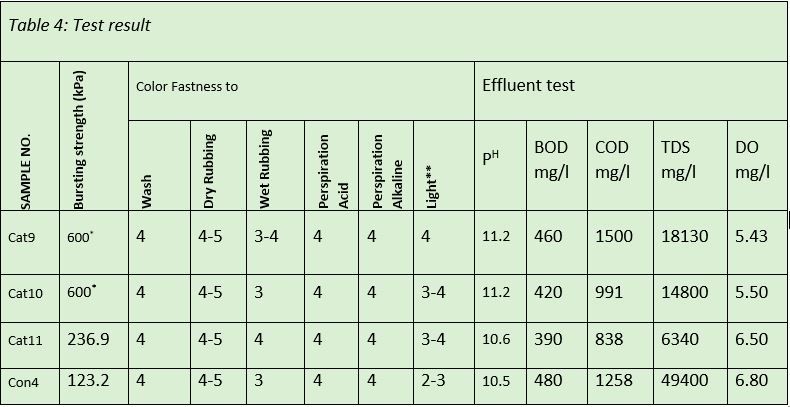
* Bursting strength is over 600 kPa
** Blue wool scale up to grade 4
Effect of cationization on color strength (K/S)
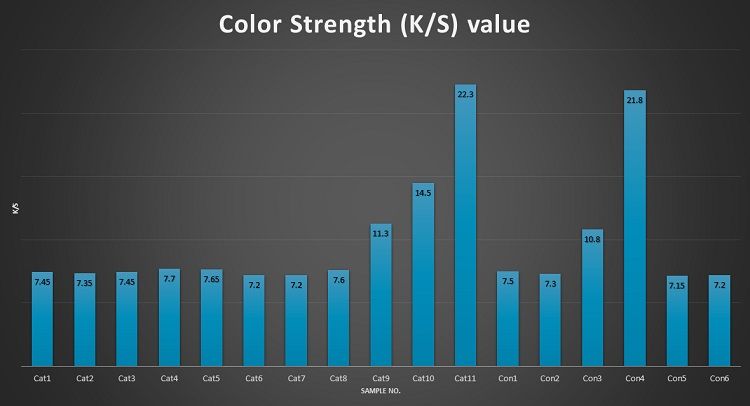
Table 3 shows that the color strength of the cationized sample is 5 to 25 percent more than the conventional sample, which ensures better color yield. The concentration of CHPTAC is positively correlated with the value of color strength. The correlation between color strength and shade% can’t be evaluated, it requires more trials and observations.
Effect of cationization on colorfastness properties
Table -4 shows that the color fastness to Wash, Rubbing (Dry), Perspiration (Acid) and Perspiration (Alkaline) are exactly equal for conventional dyeing and cationic cotton dyeing. This can be interpreted as the ionic and covalent bond formation during the cationic and conventional dyeing is almost equal in strength.
The color fastness property to Rubbing (Wet) is improved to 4 from 3 for cationic cotton compared to conventional dyeing. The better rubbing fastness for cationic cotton is the result of no unfixed dye in the fabric surface due to cationization. The color fastness property to light is also improved to 4 from 3 compared to conventional dyeing. This is due to better dye fixation and no disintegration of dye by the photon of light.
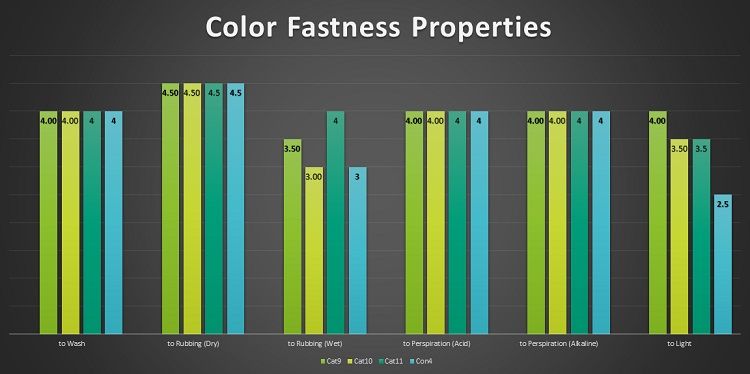
Effect of cationization on bursting strength properties
The table-4 shows that the bursting strength property for sample cat9 and cat10 is more than 600 kPa but the result of cat11 is three times lower than the cat9 and cat10. The bursting strength for conventional dyeing is unacceptable (123.2 kPa). No conclusion can be made from the data, it requires more trials and observation
Effect of cationization on environment
PH and DO (Dissolved Oxygen): Table-4 depicts that the PH and DO of the effluent are almost similar for conventional and cationic dyeing. The pH value for cationic cotton dyeing can be improved by using less Soda Ash during dyeing. The value of Dissolved Oxygen is improved with the increase of cationization chemical concentration (CHPTAC)
BOD (Biological Oxygen Demand)
The BOD indicates the degree of organic pollution in the effluent. From table -4, it is evident that the BOD value has decreased by up to 15% with the increase of CHPTAC concentration. The BOD value of cationized sample effluent is up to 18% less compared to conventional dyeing effluent. The less BOD value in the effluent indicates less environmental impact through the cationization process and better sustainability.
COD (Chemical Oxygen Demand)
COD is the measure of oxygen required for the oxidation of organic matter in the effluent. From the table-4, it is evident that the COD of the effluent has been reduced up to 40 percent with the increase of CHPTAC concentration. The COD of the first sample was 16 percent higher than the conventional dyeing.
The COD of the other two samples has been improved by 21 to 33 percent compared to conventional dyeing. This result shows that the cationization process reduces the amount of oxidizable organic materials in the effluent that will ultimately reduce the environmental impact.
TDS (Total Dissolved Solids)
TDS is the measure of all dissolved organic and inorganic substances (salt, mineral, and micro molecules) present in the effluent. It is evident from the table-4 that the TDS value decreases with the increase of CHPTAC concentration up to 65%.
The Cationization process reduces the TDS value by up to 87% as a result of salt-free dyeing and better color exhaustion. The low TDS value means fewer impurities in the wastewater and low cost in the effluent treatment plant.
The cationization process has opened the door to reuse the wastewater by reducing the TDS by a significant amount. This is a turning point for environmental sustainability.
Cost calculation
Note: The costing is estimated, the actual costing is a commercial issue. The cost may change with time, type of machine, and operational excellence.
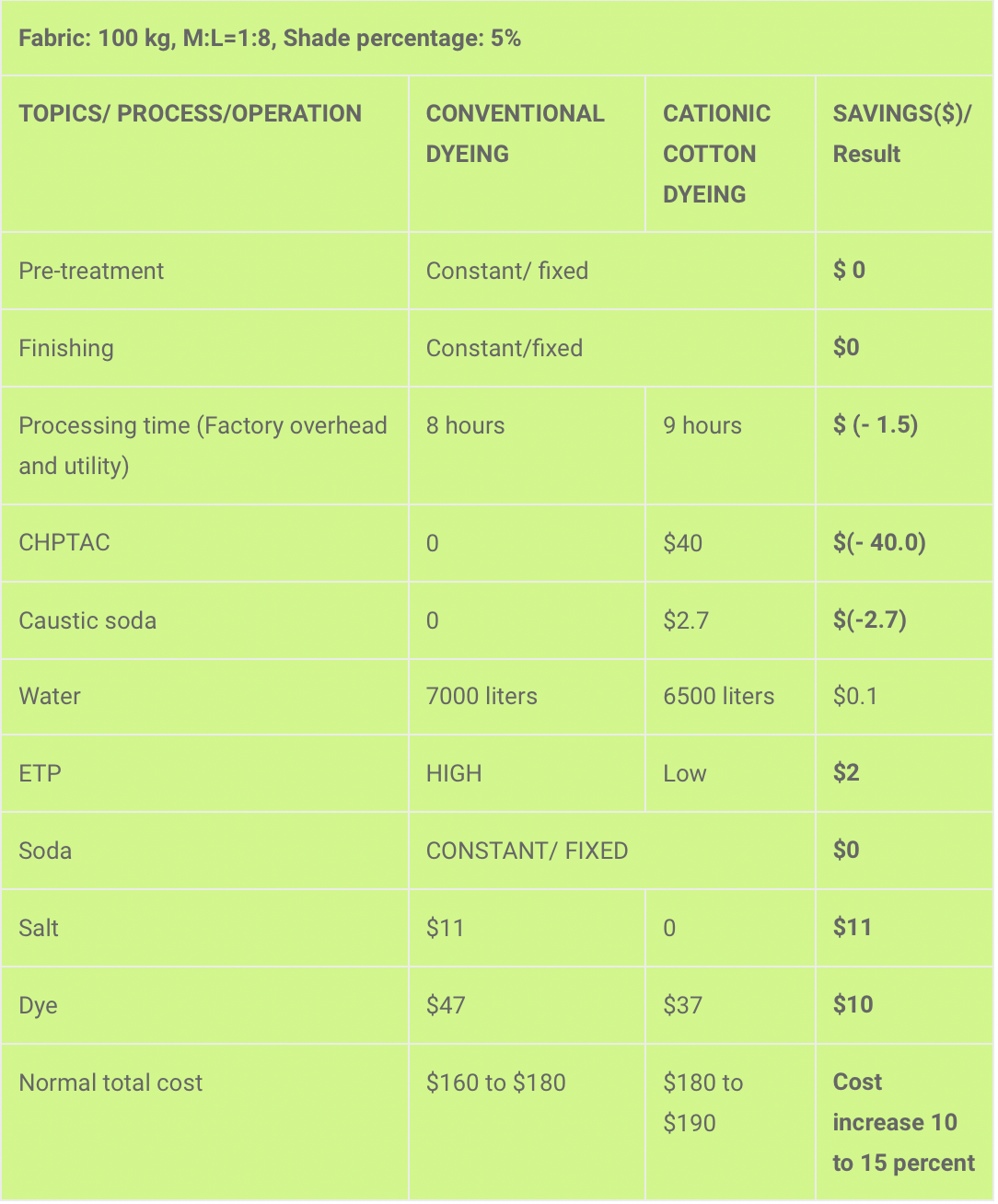
Conclusion
The cationization of cotton for commercial dyeing is a piloting project in Bangladesh. The result of the study shows that the cost of the total process will increase 10 to 15 percent, which is challenging for commercial applications.
Although the cationization of cotton gives better color yield, improves dye takeup, reduces water use, and reduces the ETP load, it is challenging because of the high price of cationization chemicals (CHPTAC).
In concern of sustainability cationization of cotton can play an important role in commercial dyeing because it ensures less environmental impact. Though the cost is slightly higher, the quality improvement and sustainability issue can offset the extra cost.
Further research and development can reduce the cost by improving the process/ product or substituting the costly chemicals with cheaper ones.
References
Broadbent, A. D. (2001). Basic principles of textile coloration. Society of dyers and colorists.
Burkinshaw, R. S. (2002). A greener approach to cotton dyeings with excellent wash fastness. Royal Society of chemistry.
Burkinshaw, R. S. (2003). Treatment of cellulose with cationic, nucleophilic polymers to enable reactive dyeing at neutral pH without electrolyte addition. Journal of Applied polymer science.
D.P. Chattopadhyay, R. C. (2007). Salt-free reactive dyeing of cotton. International journal of clothing science and technology.
Fraze, L. (2002). A cleaner way to color cotton. Environmental Health Perspectives.
Lewis DM, V. L. (2007). Dyeing cotton with reactive dyes under neutral condition. Wiley online library.
- Montazer, R. M. (2007). Salt-free reactive dyeing of cationized cotton. Fibers and Polymers.
Mohamed Hashem, P. H. (2003). Reaction Efficiency for Cellulose Cationization Using 3-Chloro-2- Hydroxypropyl Trimethyl Ammonium Chloride. SAGE Journals.
Nallathambi Arivithamani, V. G. (2018). Characterization and comparison of salt-free reactive dyed cationized cotton hosiery fabrics with that of conventional dyed cotton fabrics. Journal of Cleaner Production.
Ristic, N. R. (2012). Cationic Modification of Cotton Fabrics and Reactive Dyeing Characteristics. SAGE Journals.
Sanjit Acharya, N. A. (2014). Chemical cationization of cotton fabric for improved dye uptake. Springerlink.
Tabba, P. J. (2006). Improving the environmental and economic aspects of cotton dyeing using cationized cotton. Textile Institute’s 80th World Conference, Manchester. Manchester: Wiley Online Library.
The Dow Chemical Company, M. M. (2009). CR-2000 Cationic Reagent Product Technical Data. Midland, Michigan 48674 U.S.A.: The Dow Chemical Company.
Wang, L. /. (2009). preparation of cationic cotton with a two-bath pad-bake process and its application in salt-free dyeing. Carbohydrate Polymers.